(1)金屬鎂冶煉金屬鎂冶煉有熔鹽電解法和熱還原法兩大類,其中熱還原法有皮江法和半連續法兩種。我國絕大多數鎂生產廠家采用皮江法。
鎂金屬冶煉主要在原料(礦石和石油焦)準備和加工過程中產生粉塵。
(2)鈦金屬冶煉海綿鈦生產均采用鎂還原法,其中主要是鎂還原—真空蒸餾。鈦白(二氧化鈦)的生產方法有硫酸法和氯化法兩種,其中氯化法發展較快。
鈦金屬冶煉產生粉塵的工序是原材料(鈦礦渣、石油焦、瀝青)的轉運、破碎、研磨以及鈦渣熔煉。
2.鈦渣燃煤煙氣除塵系統設計
(1)煙塵特性高鈦渣電爐技術參數和煙氣特性如下:
1)煙氣溫度:200~400℃;
2)煙氣成分:CO2占15%~18%;N2占25%~78%;O2占5%;H2O占2%。
3)煙塵濃度:2~6g/m3(標準狀態);
4)粉塵堆積密度:200g/m3;
5)煙塵比電阻:3.3×1012~5.5×1014Ω·m;
6)煙塵粒徑見表13—56。
表13—56高鈦渣煙塵粒徑分布
粒徑/μm | >74 | 74~63 | 63—53 | 53~44 | <44 |
所占百分數(%) | 40 | 8 | 8 | 6 | 38 |
表13—57高鈦渣電爐的排煙量
爐容/kVA | 爐氣量/(m3/h)(標準狀態) | 設計排煙量/(m3/h) | 煙氣溫度(冷卻后)/℃ |
12500 | 70000 | 110000 | 180—200 |
9000 | 48600 | 85000 | 180~200 |
6300 | 35000 | 61000 | 180~200 |
3500 | 23000 | 35000~40000 | 180~200 |
(3)除塵工藝鈦渣熔煉電爐排煙方式采用半封閉式矮煙罩,罩口距電爐口約1.8m。先借助熱交換器冷卻煙氣并回收余熱,再以袋式除塵器凈化。
注意:須嚴密監控袋式除塵器人口溫度,既防止其過高,也防止其低于140℃。
3.工程實例、
【常源機械實例】內江威遠某鋼鐵集團有3臺高鈦渣電爐,容量均為6500kVA。每爐煙氣量為61000m3/h,煙氣溫度為180~230℃(冷卻后溫度),含塵質量濃度為3.1/m3(標準狀態)。合并設計一個集中除塵系統,處理煙氣量約為190000m。/h。其工藝流程如圖13—36所示。
高鈦渣電爐煙氣進入u形冷卻器降溫并沉降大顆粒,然后進入袋式除塵器凈化,并經煙囪排人大氣,收集下來的煙塵包裝后外運。
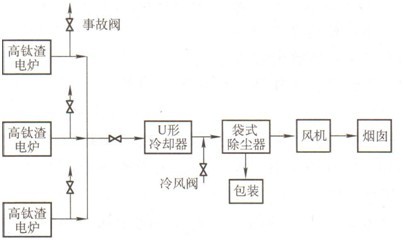
圖13—36高鈦渣煙氣凈化工藝流程
該系統的袋式除塵器選型時考慮兩種方案:反吹風袋式除塵器和長袋低壓脈沖袋式除塵器。兩種除塵器的主要規格和參數見表13—58。經比較后,采用第二方案。
表13—58兩種袋式除塵器的規格和參數
名稱 | 方案一 | 方案二 |
型式 | 反吹風袋式除塵器 | 長袋低壓脈沖袋式除塵器 |
處理煙氣量/(m3/h) | 190900 | 192700 |
濾袋材質 | 玻纖膨體紗濾布 | 玻纖針刺氈 |
過濾面積/m2 | 7400 | 4400 |
過濾速度/(m/min) | 0.43 | 0.73 |
每臺電爐的排煙管道設電動放散閥、管道系統閥和混風溫控閥。
選用2臺鍋爐引風機,型號為Y4—73—11№14D,風量為100000m3/h,全壓為3940Pa,電機功率為185kw。
該系統運行兩年多后,效果仍然良好。
關于更多除塵器設備的介紹,您可以查看:http://www.uadw.cn/chuchenqi/